6月25日,由電池中國網主辦的第15期“Li+學社”大講堂在廣州舉辦。重慶長安新能源汽車科技有限公司電池專家楊輝前,做了關于“新能源汽車電池系統安全問題分析及解決對策”的技術分享。
圖為重慶長安新能源汽車科技有限公司電池專家楊輝前在Li+學社做專題報告
楊輝前談道,電芯能量密度高和體積變大會帶來一些問題,比如內部發熱多、散熱困難,以及熱失控噴發非常劇烈等。所以應對策略之一就是,將溫度的布點增多以及時全面捕捉電池溫度的變化,同時還要增加熱管理系統的效率,比如升溫和降溫的速率,導熱的效率等。
對于熱失控,需要進行全方位的防護,這其中電芯之間的隔熱非常重要。對于電池“不起火”的說法,楊輝前認為有時候是個偽命題,最大的挑戰在于電芯熱失控時噴閥方向的不確定性,電芯的六個面都有可能噴閥,尤其是電芯底面防護困難,代價高,只有在設計上能確保電芯熱失控噴閥位置和方向的唯一性,即只從電芯的防爆閥處噴發,電池包的防護上才是完全可控的,代價可接受的,本質上有解的,“不起火”才終將“貨真價實,言行一致”。
對于電池熱失控該如何排氣,楊輝前表示,我們認為安全首先是對人的安全,對人的安全是第一位的,我們的理念是熱失控的時候電池包只能從規定的地方排氣,即從電池包防爆閥定向排氣,不允許從其他的位置排氣,只要從其他位置漏氣測試就是失敗的,同時要避免熱失控氣體進入車內,熱失控氣體中有40%左右都是一氧化碳,容易吸入中毒。
楊輝前指出,大數據監控對于及時發現電池安全隱患問題非常重要,通過“治小病來防大病”,在電池全生命周期的使用過程中,電池有任何異常放電,或自身耗電電量降低的一致性變差的行為,都希望能夠及時通過大數據監控到,然后把它從車上拆下來,排除潛在不安全的隱患,接著對舊件進行返廠分析原因,返回到生產線工藝過程上找尋根本原因,分析問題到底是怎么產生的并加以改進,以不斷提升后續產品質量。
BMS及大數據算法應用好的基礎前提是數據質量和顆粒度,要確保各個信號包括總電壓、總電流、單體電壓等嚴格意義上同步。因為電池本身的反應速度皮秒級,而采樣系統目前最多能做到十微秒級。各家芯片采樣速度不同,采集一路需要幾十到幾百微秒不等,加之許多單體采樣芯片是串行的,一般有6~18路,即使系統上做到各芯片同時啟動采樣,但各芯片采樣的第一路和最后一路也差別了較長時間,有的差幾毫秒。在總電流快速變化時,同一時刻采集的電壓壓差較大,比如200A充放電時,本來電池實際的動態壓差在20mV以內,但因采集芯片串行采樣的不同步,動態壓差可能會超過100mV,甚至更大,這需要與單體電壓采集芯片廠家一起再努努力,意識到同步采樣的重要性,真正做到每個單體電壓信號采樣甚至包括總電壓、總電流和溫度都是嚴格意義上的完全同步。這或許又是一次行業巨大的技術革命,這樣就可以發現和驗證電芯內部更多的有趣的預想規律,可以排除更多的潛在隱患,市場車輛電池熱失控發生率將明顯大幅減少。
楊輝前表示,怎么避免極耳焊接的焊渣是非常重要的,因為有些焊渣掉在電芯頂部很不容易被檢出,但有時候會壞事,是否會導致電芯的“猝死”還未強關聯,但至少從各種可能觸發電池熱失控條件的組合試驗來看,極片間的正負極鋁箔銅箔硬短路是最劇烈的不停歇的,而且在數據上表現不一定明顯。通過對電芯合格成品再度抽樣進行頂部X-Ray拍片,逐個仔細比對照片色差變化發現,偶發會有微小顆粒存在,但與設備廠家交流,達到能自動識別和篩選還有一定難度;同樣,抽取一定量的入殼絕緣合格但頂蓋還未焊接的電芯倒置抖動,偶發也會有微小顆粒焊渣存在,這對電芯而言是非常不利的,是顆不***。對于大電芯可能更是未來的一種挑戰,連X-Ray設備都將無法使用,希望能加強相關設備的檢出能力或改進焊接工藝,避免焊接時焊渣飛濺落入或重力落入。
“對于電池熱失控報警,在時間層面來說,主要是將報警的時間縮短提前,因為一旦發生熱失控之后,電池系統內部溫度會特別高,尤其是靶芯靠近BMS時,如果時間長了,可能整個系統就不能正常工作了,會漏報;在電池箱體的防護上需要將時間延長,確保熱失控過程中密封不失效,氣體和熱量有序可控,達到‘不起火不爆炸’的目的。在預警上,我們開發了24h在線巡檢功能,任何時候電池電壓和溫度的微量變化都將被捕捉,一旦有熱失控的趨勢,就會預警,將進行快速市場處置行動?!睏钶x前指出。
圖為“Li+學社”技術交流現場

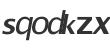